
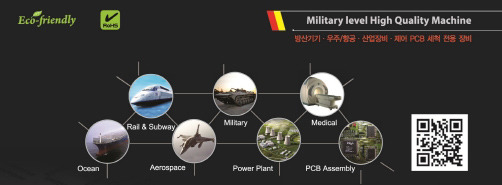
n ÀåºñÁ¦¿ø ¹× Ư¡
1. Visualization of the whole process :
Cleaning room equipped with visual window, cleaning process be clear at a glance.
2. The world¡®s largest cleaning baskets :
645mm(L)¡¿560mm(W)¡¿200mm(H) 2 layer , Meet larger PCBA sizes and higher
cleaning production.
3. The most scientific nozzle design :
Increasing nozzles from left to right Enhance the cleaning efficiency£¬Distribution nozzles
up and down. Completely solve the blind clean area.
4. Nozzle pressure adjustable design :
Solve the small size of PCBA in the cleaning process by spray under high pressure collision,
splash problem.
5. With standard diluent slot heating system :
Greatly promoted cleaning efficiency. Shorten cleaning time.
6. Touch screen interface :
According to different PCBA model set with different process parameters,
Quick edit and variety of different process parameters can be stored program, including
solvent temperature, cleaning time, rinse times/time, rinse temperature, dry time,
drying temperature, conductivity monitoring parameters, etc.
According to different permissions, operator, can be set password management authority.
7. High standards of cleanliness :
Ion pollution completely accords with the 610D IPC-¥° class standard
( less than 1.5 ug/cm2, and the U.S. army standard of MIL28809 ¥° class standard
8. Convenient liquid add mode :
Can manual to join, also can set according to proportion (5% ~ 25%) automatic proportioning
D.I water and chemical fluid.
9. Special spray tank and auxiliary heating system :
Spray liquid tank is storage liquid in cleaning and rinsing process ,inject liquid into spray tank
by dilution tank and continue to heat ,through high pressure pump to spray out, spray liquid
tank is storage DI-water in rinsing process ,and also through high pressure pump to spray,
can be choose heating or not.
10. Lower running cost :
Built-in filter device can achieve solvent recycle, reduce solvent dosage, The end of the cleaning
by compressed air recycling pipeline and pump residual liquid, it could be save 50% liquid.
11. The cleanness of real-time monitoring system :
For monitoring cleaning effect, Resistivity meter can be set and the scope is 1M¥Ø£15M¥Ø.
12. More environmental friendly and zero-emission :
built-in rinsing liquid emissions filtering system effective filter cleaning process to produce
a variety of impurities, COD, BOD, PH reached safety environmental emissions.
n Technical Data :
1. Clean Basket Size : Max 645mm(L) ¡¿560mm(W) ¡¿ 100mm(H) 2 layers
2. Dilution Tank Capacity £º Max 60L
3. Concentrate Tank Capacity : 30L
4. Spray Tank Capacity : 17L
5. Cleaning method:360¡ÆWhirl / Ejection for cleaning : hot air for drying
6. Cleaning Time : 5~30 Minutes ( Reference )
7. Cleaning Liquid Isolation Time : 1~3 Minutes
8. Rinsing Time £º 1 - 2 Minutes ( Reference )
9. Rinsing Times : 1 - 99 (Set£©
10. Drying Time : 20~40 Minutes ( Reference )
11. Cleaning Liquid Recovery Filter£º 1¥ìm ( filter tiny impurities: solder paste, flux, rosin and pollutants )
12. Rinsing Liquid Discharge Filter £º5¥ìm ( filter tiny impurities: solder paste, flux, rosin and pollutants )
13. Dilution Liquid Heating Temperature£ºRoom temperature¢¦60¡É
14. Drying Heating Temperature£ºRoom temperature¢¦90¡É
15. Resistivity Meter Monitoring Range £º 1M¥Ø¢¦15M¥Ø
16. D.I Water Supply £º 30¢¦60L/min
17. D.I Water Pressure£º ≦0.4Mpa
18. D.I Water Entrance Pipe Connection£º 3/4 inch
19. Dilution Liquid Heating Power £º 9KW
20. Air Supply £º0.45Mpa~ 0.7Mpa
21. Air Consumption£º200-400L/Min
22. Power Supply £ºAC380V 50/60HZ 65A
23. Net Weight £º600Kg
24. Exhaust Size £º¥Õ100mm(W)¡¿30mm(H)
25. Machine Size £º1200mm(L) ¡¿ 1000mm(W) ¡¿ 1800mm(H)

n ¼¼Ã´±â Àåºñ ºñ±³Ç¥


 |